HUSQVARNA
Drill Motor
HUSQVARNA
INDUSTRIAL DESIGN
Year 2018
Role Industrial Design Lead
Studio Husqvarna Group (in house / SWEDEN)
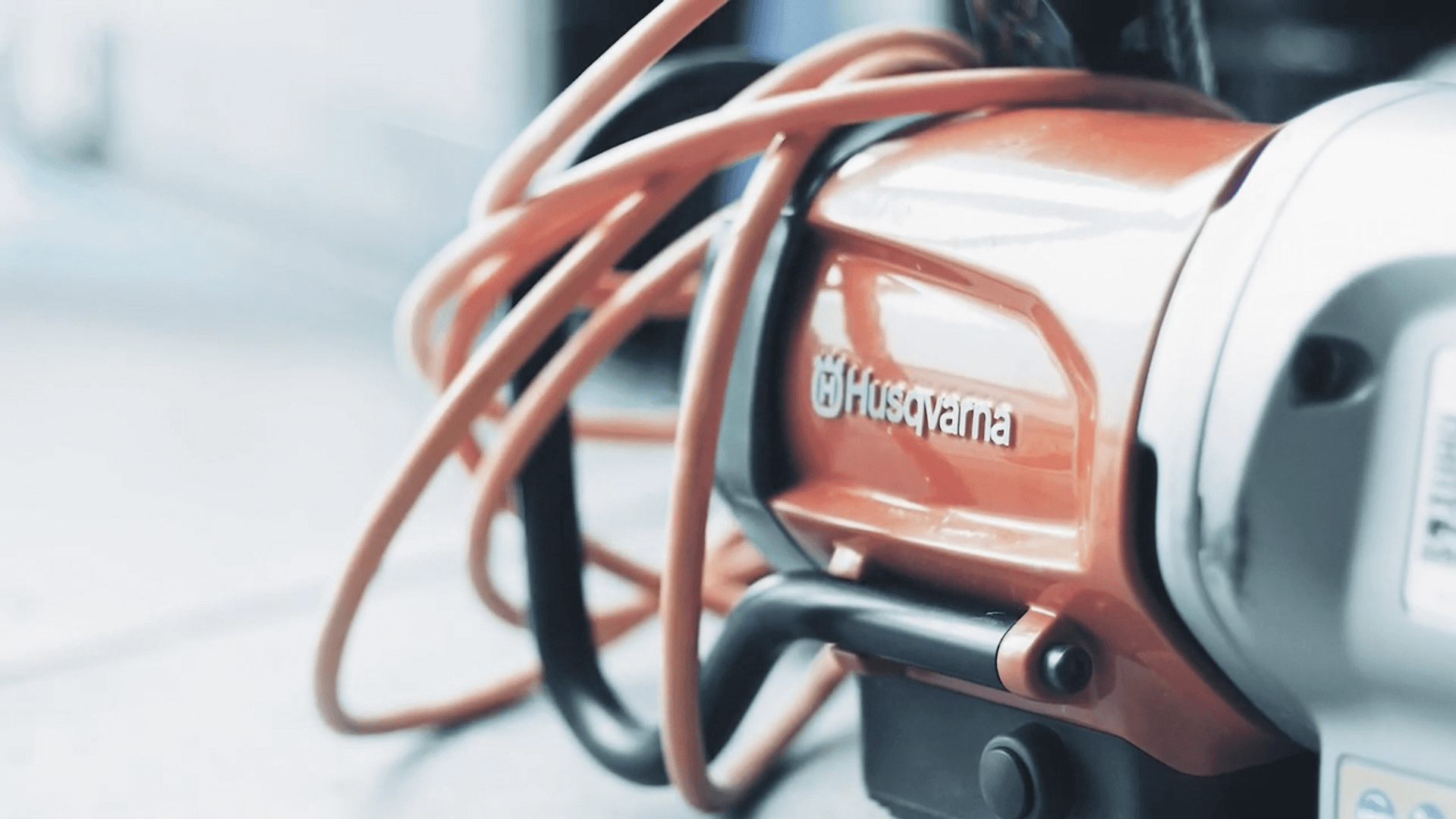
A new drill motor redesign and rebuild from scratch.
The motive for the project was to make the Husqvarna's small drill motor business profitable. We've been asked to replace the old products that they had quality issues with, by new machines that have been developped by R&D and proved to be very reliable and powerful. The challenges were the very fast time to market restriction, and the need to work around the available package to not add complexity and involve more R&D work than necessary. The success criteria was an easy to assemble machine, with a design that integrates all sealing surfaces and seals available to keep the same performances. The machine was unveiled at the "world of concrete" expo of Las Vegas in January 2020.
My role as an industrial design lead has been to deliver a design that fits the Husqvarna DNA around a very restricted package. The project was mainly driven by mechanical restriction and manufacturability constraint, I therfore acted as a tampon between our R&D and our project management that wanted the product as fast as possible on the market. The biggest challenge was to be able to deliver a strong design without changing any single screw position nor sealing surface while keeping the air flow and cooling proprietaries already achieved in the R&D prototype.
Credits Lukas Mathson, Surface Designer
Credits Anders Erestam, Engineering Lead
Credits Gustav Landberg, Brand Design Manager Husqvarna Construction
Credits HÃ¥kan Pizani, Global Product Manager
Credits Caroline Bergström, Project Manager
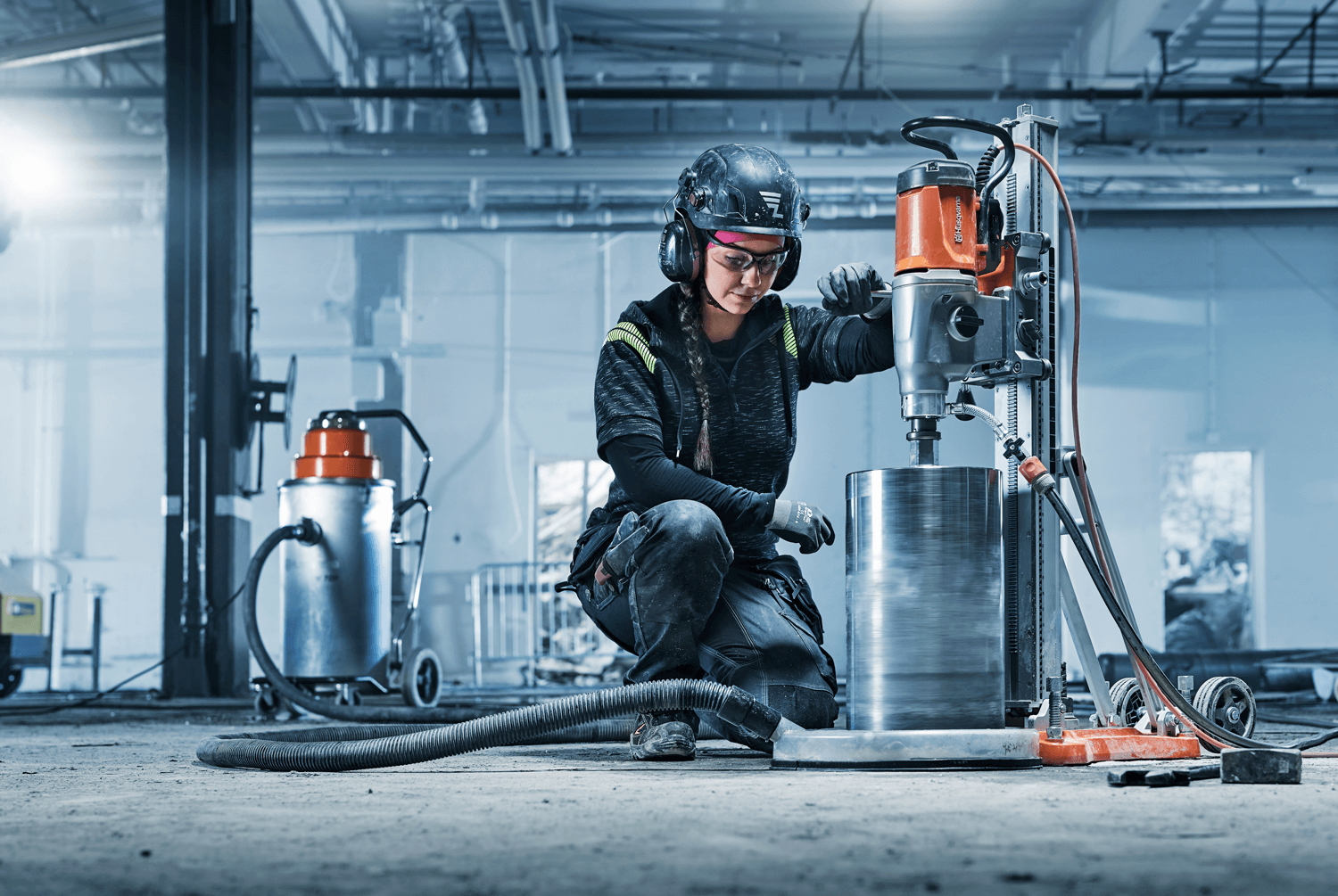
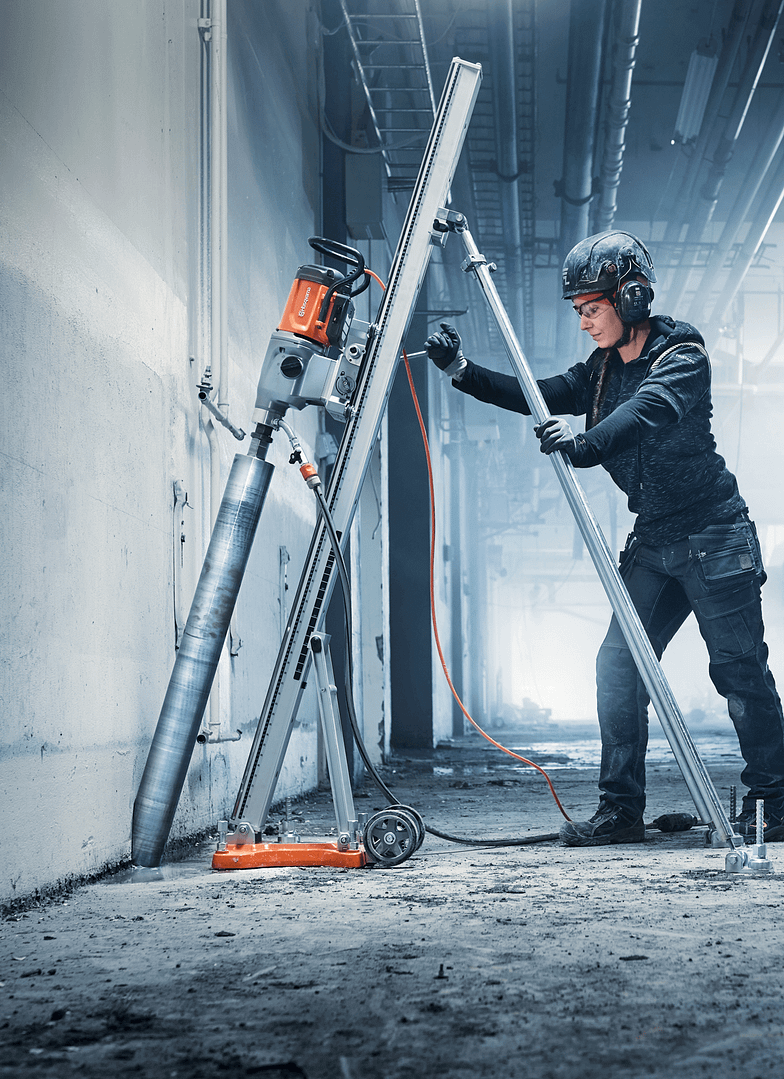
Trustworthy attitude.
The lines of the machine communicate dynamism and compactness. Yet the machine looks robust. The choice of material such as the complete aluminium casing provides an extra premium feeling of quality and durability. All this is aimed to make that product a reliable choice for our customer.
From set up to result in no time.
Lightweight, compactness and durability were the key attributes when designing Husqvarna DM 400. But most importantly the machine needed to be easy to set up and use. The drill motor is the central part of a full drilling system where all of the components work together perfectly. Therefore our product has been build to be quickly snapped on and off the column to allow users changing position whenever he needs.
The design of the machine has been grandly driven from usability perspective. Flat surfaces on top of machine, size and shape of the handle for holding from anywhere as well as the feet design and snapping connection with the drill stand connector. The purposeful design allows work close to walls and corners.
Redesigned to withstand the toughest environment, the machine put the effort on the durability. The servicing is an important factor for those products which get rough headling on daily basis. The design was thought through to allows the machine to be quite easy to open and service.
From usability perspective we focused on providing a user friendly tool to operators. We, for example, implemented the handle system for transportation purposes and durability.
We wanted the product to look compact and integrated through shapes and volumes that interlock with each other. Especially when the competition usually has very straight splits. The dynamic lines and focus down is given to communicate a sense of precision as well as visualizing the power inside the machine and show how it is pushed down into the ground through the drill bit.
From Rendering
to Reality
The final product has kept 90% of its latest design concept before hitting production. The main changes we had to operate was about the handle and logo as we encounter some issue with our supplier and manufacturing techniques.
R&D package
Engineering package was already set up from the beggining as those machines require strict and reliable machanism. The design mission was to improve usability and create design language around the package without compromizing its original purpose.
Ergonomy Testing
Volume blocking and improved usability. Once the first sketchs and directions were set, I printed some main bodies to physically interact with machine, get a better understanding of volumes and validate ergonomy of overall machine.
Prototyping
Once we validated the ergonomy and design detailing, we made a prototype to check the compatibility with the internals and go through user testing. Gauging performancewith new body as well as weight and prehension.
Testing
Development on the connectivity part and electronic box, made us tweak the design several times for the UX as the space and placement of components made us take compromises between usability and aesthetics.
Process
This project was very technical and R&D driven, for this type of machine, air flow and performance are key for a successful product. Therefore the design limitations were quite important and it quickly became a challenge to offer appealing design without impacting the internals or the air flow. Some pretty renderings were created to validate design direction in design reviews but 90% of the work was quick sketches and CAD iterations.
In this project R&D and design were established in 2 differents geographic location. The main factor for success was communication. We exchanged a lot over skype, screenshoot every bits of the product and drawing on top. Often, the focus wasn't on being pretty but rather just being understandable.
DM 400 is designed for rough handling and heavy drilling jobs, but it is also very easy to handle regardless of working conditions. It is really reliable work horse, built to make the operator proud of his work.
HÃ¥kan Pinzani,
Global product manager, core drilling systems.